Do you know where your clothes come from?
Take a moment to go through your closet and look at the tag stitched into the collar of your favorite cotton t-shirt. Notice anything similar?
Chances are that more than half of the items in your wardrobe have the words “Made In China” or “Made In Vietnam” on the tag. And where you don’t find either of these, you’ll almost always see Indonesia, Mexico, Italy, Honduras, India, Thailand, or Bangladesh– essentially anywhere other than the USA (1).

In America circa 1980, at least 70% of our clothing was made in the USA. Now, that majority stake in our closets has plummeted to 3% (2).
Where Did Clothing Made in the USA Go?
The “Made in” tags document the history of a fallen domestic textile industry and, along with it, a truly sustainable supply chain for apparel as the industry went abroad in search of cheaper labor and materials.
America’s once-robust textile industry employed 1.3 million workers across hundreds, if not thousands of mills (3). However, from 1990 to 2011, roughly 750,000 apparel manufacturing jobs in the U.S. vanished (4).
Beginning in the mid-1970s, economic development in Asia and Central America saw the emergence of massive textile mills that offered US-based apparel companies access to untapped production capacity, powered by fractionally expensive labor and material. These mills were everything they promised, fulfilling larger and larger orders with increasing efficiency and cost-effectiveness.
By 1980, major US-based chain retailers like Gap Inc. and J.C. Penney recognized the opportunity to permanently cut costs by redesigning their business models around the wholesale off-shoring of all manufacturing to low-cost, high-capacity mills.
As these hugely influential companies explored the new landscape of foreign apparel manufacturing in the 80s and 90s, they found additional opportunities to reduce costs by sending garments to different factories and countries for individual steps in the production process based on where costs were lowest. In fact, in 2004 Gap reported that it sources from roughly 3,000 factories in about 50 countries, mostly developing nations (5).
The Threads Between Offshore Manufacturing + Fast Fashion
This compartmentalization of off-shored apparel production initiated in the 1990s planted the seeds for the extremely intricate, yet agile and inexpensive, supply chains that major US apparel retailers depend on today to stock their shelves with what we now call fast fashion.
As cotton apparel and textile manufacturers continue to double-down on cost-cutting measures, they pass these savings on to insatiable consumers back home in America in the form of fast fashion clothing that dominates retail spaces.
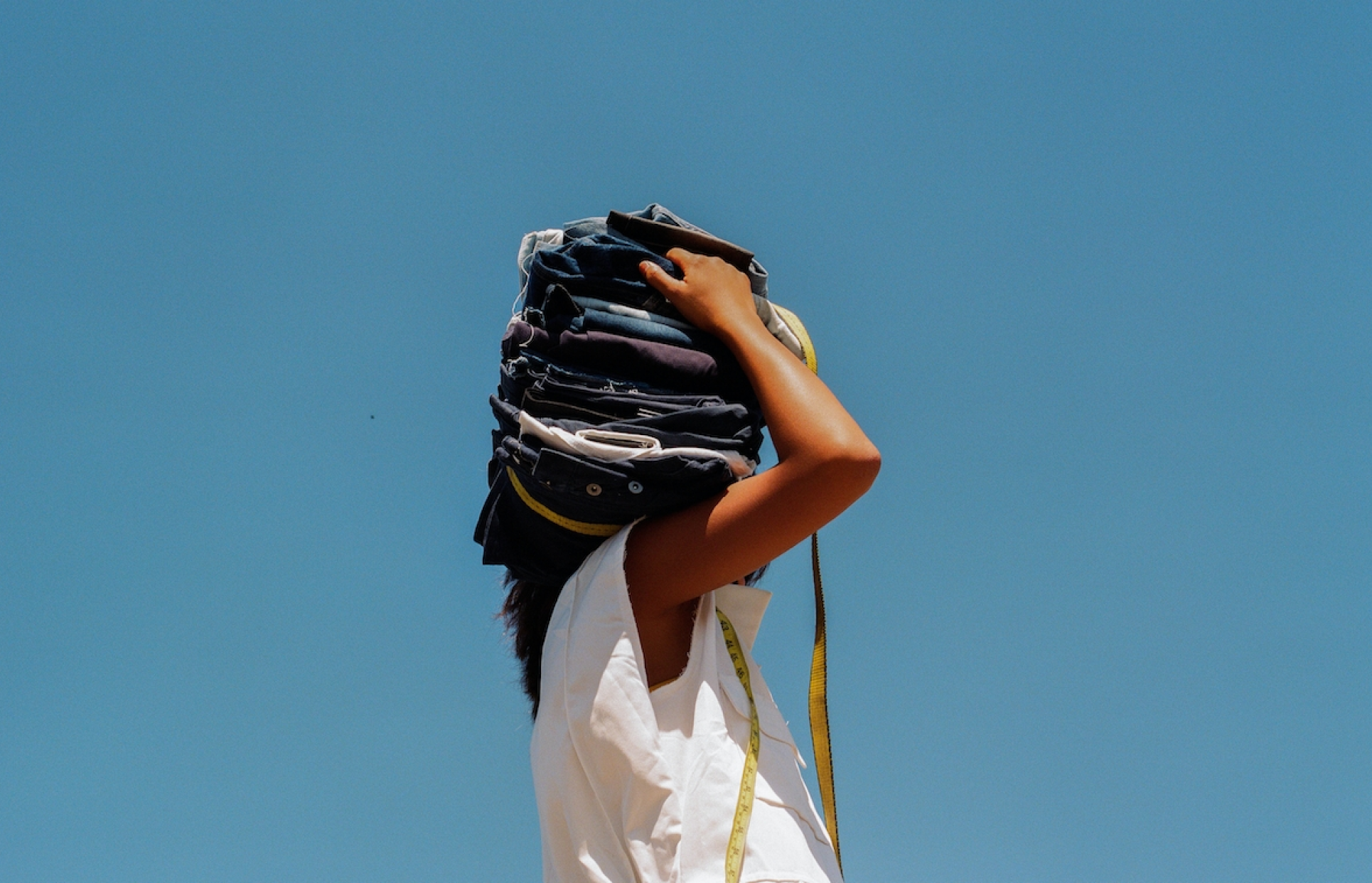
In 2020 alone, the US imported cotton textiles and apparel valued at over $127B, with year-over-year growth since 2016 (6).
How Sustainable Is Fashion’s Cotton Apparel Supply Chain?
What’s the hidden cost of relocating the production of cotton clothing once made in the USA to the far reaches of the globe? The answer is twofold: significant, but largely avoidable, contributions to climate change resulting from the deprioritization of true innovation within the cotton apparel industry.
The staggeringly complex and increasingly precarious supply chains involved in offshoring cotton apparel production guarantee a steady stream of emissions-based carbon into the environment.
Beyond the emissions from transportation, which represent just 3% of fashion’s total greenhouse gas (GHG) contributions, the more significant environmental costs emerge from the linearity of fashion’s deeply entrenched “point A to point B” physical infrastructure that recreates itself in the mentality of brands and consumers alike (7).
Under the current model, cotton apparel is made there and comes here. When we wear out or no longer want a particular garment, we discard it without a second thought because we can always purchase more of the >$127B worth of cotton apparel manufactured abroad and imported to the US each year.
The moment we toss out a piece of cotton clothing it effectively reaches the end of the line within today’s prevailing linear mode of production and consumption. And what does the end of this linear process actually look like? Quite literally, the dumps: massive landfills and industrial incinerators.
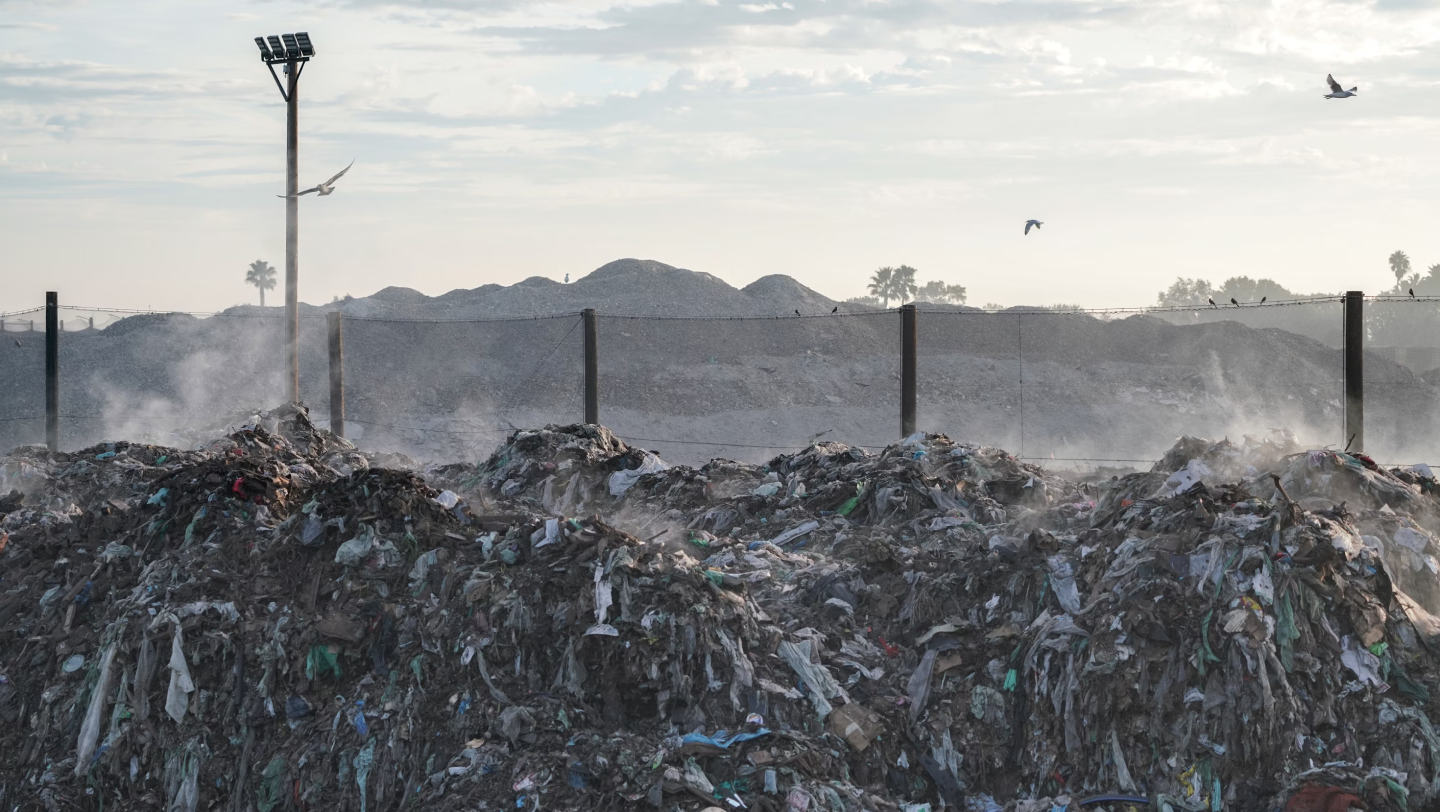
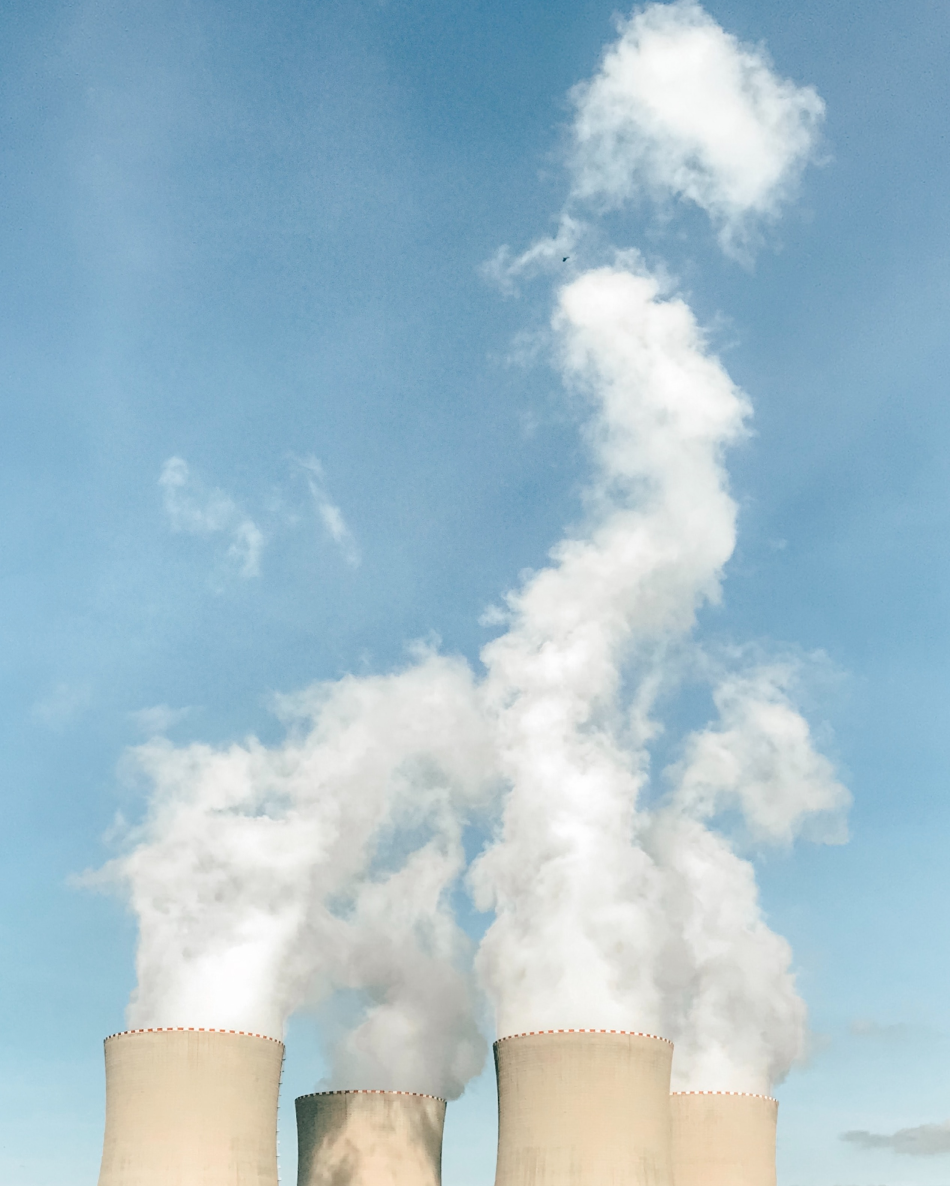
How Linear Manufacturing is Harming the Planet
EPA data shows that in 2018, the US generated over 17 million tons of textile waste, predominantly consisting of unwanted clothing, of which an astounding 85% ends up in landfills or is burned (8).
This overwhelming loss of material to the terminal point of fashion’s linear manufacturing systems and thinking requires non-stop – and likely increasing year over year – cultivation, processing, and manufacture of new cotton materials.
It’s these largely uninterrogated upstream processes that generate the lion’s share (38%, according to a 2020 McKinsey paper) of fashion’s carbon and other GHG emissions (9).Together, the production (38%) and transportation (3%) of cotton for apparel and textiles account for up to 41% of the sector’s total climate impact.
With the fashion industry accounting for roughly 4% of total global GHG emissions, there’s a dire need and opportunity for innovative solutions to establish a new, actually sustainable supply chain for cotton clothing (10).
Embracing Textile Circularity: The Future of Sustainable Fashion
The fashion industry, and the world, need true cotton textile circularity: recycled and recyclable clothing made from the cotton goods already here in the USA.
Such innovation can’t limit its efforts to merely breaking up the linear logic and flow running throughout the entirety of the cotton goods value chain. It must go further. It must then pick up the pieces of this already broken system, reevaluate them, and intentionally reconnect them to transform the finite line from production to destruction into a virtuous cycle of production to re-production.
In short, embracing textile circularity means rethinking how we produce, consume, and dispose of cotton apparel, ensuring a sustainable future for the fashion industry. And Everywhere Apparel is doing just that.
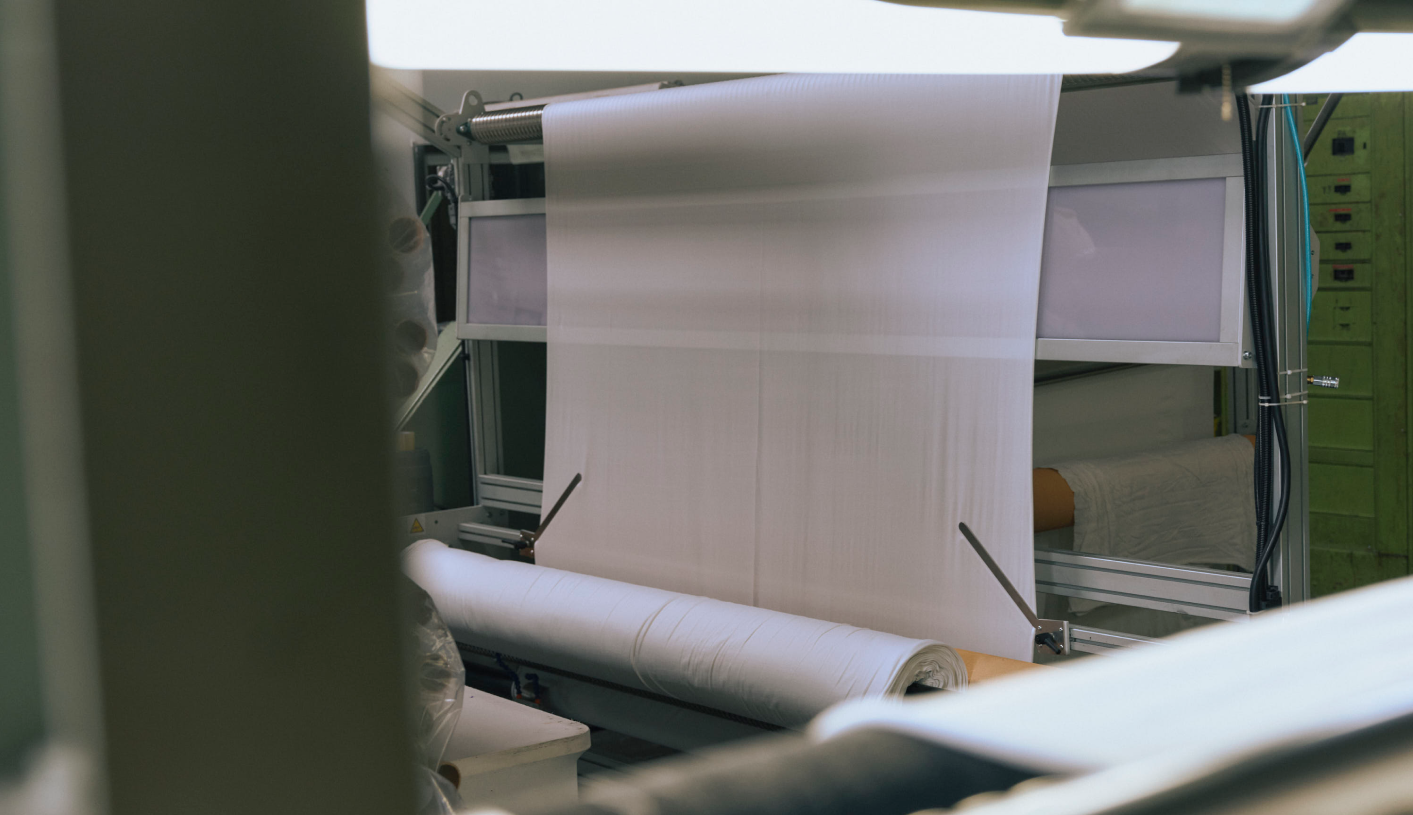
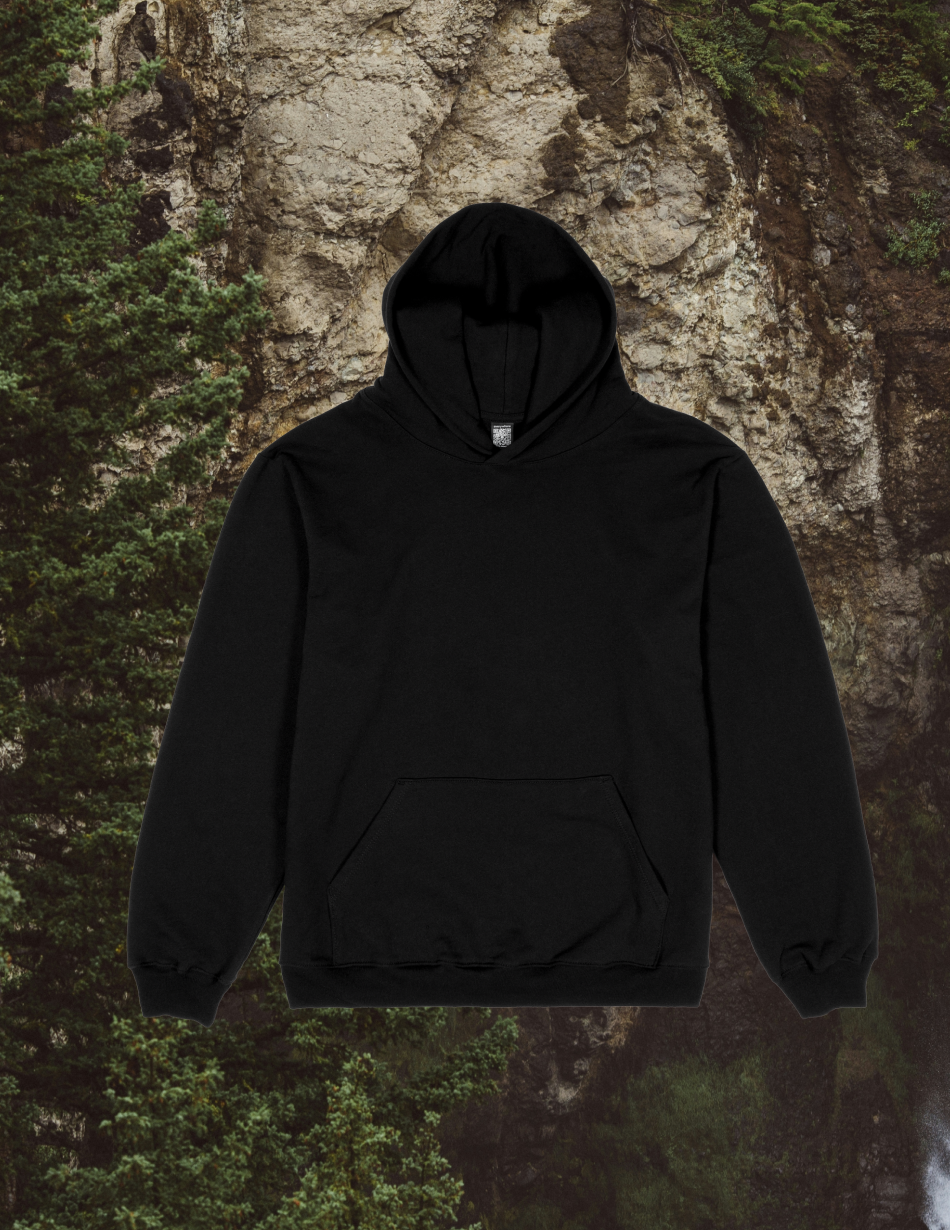
Why Everywhere’s Recycled Cotton Clothing Is Always Made in the USA
By producing apparel domestically from recycled cotton in our LA-based facilities, Everywhere Apparel, our brand partners, and consumers all benefit from a more controlled and transparent supply chain. This approach reduces transportation emissions, supports local jobs, ensures higher quality standards, and lays the groundwork to create hyper-local ecosystems where apparel can be produced in the same place it was consumed.
Moreover, we’ve strategically partnered with top-tier organizations like Material Return, Cotton Inc., and the Gaston College Textile Laboratory to ensure we maintain a steady supply of sustainable materials, continuously improve our recycling processes and product quality, and conduct rigorous testing and quality control on all of our recycled cotton products. These efforts help guarantee that each item we produce meets the highest standards of durability and sustainability.
Our partnerships with leading US-based institutions in textile research, sourcing, quality control, recycling, and product development foster collaborative innovation around cotton apparel recycling and manufacturing processes.
Together, we’re paving the way toward a more sustainable and circular fashion industry.
Sources
- BCG. The Future of Fashion Sourcing.
- The Atlantic. Some Damn Fine Shoes.
- Monthly Labor Review (Aug 1995). Unraveling Employment Trends in Textiles and Apparel.
- U.S. Bureau of Labor Statistics. Fashion.
- NBC News. Gap reports widespread labor violations.
- United States International Trade Commission. Textiles and Apparel.
- McKinsey & Company. Fashion on Climate.
- United States Environmental Protection Agency. Textiles: Material-Specific Data.
- McKinsey & Company. Fashion on Climate.
- Ibid.